How Plastic containers are made, And What is Plastic Molding machine.
- Haitian
- Apr 9
- 4 min read
Updated: Apr 15
Our everyday lives are filled with plastic containers, which are necessary for storing food, drinks, home goods, and other items. The efficiency and adaptability of plastic manufacturing methods are demonstrated by their extensive application. Plastic molding machines, which use a variety of molding techniques to turn raw plastic ingredients into completed products, are essential to the production of these containers. This thorough investigation explores the sorts of plastic molding machines used, the production procedures for plastic containers, and the crucial function that plastic molds play in the plastics sector.
Comprehending Plastic Molding Equipment
Plastic molding machines are specialized pieces of machinery used to use molds to shape molten plastic into desired shapes. Because they allow for the mass manufacture of reliable, high-quality plastic goods, these machines are essential to the plastics industry.
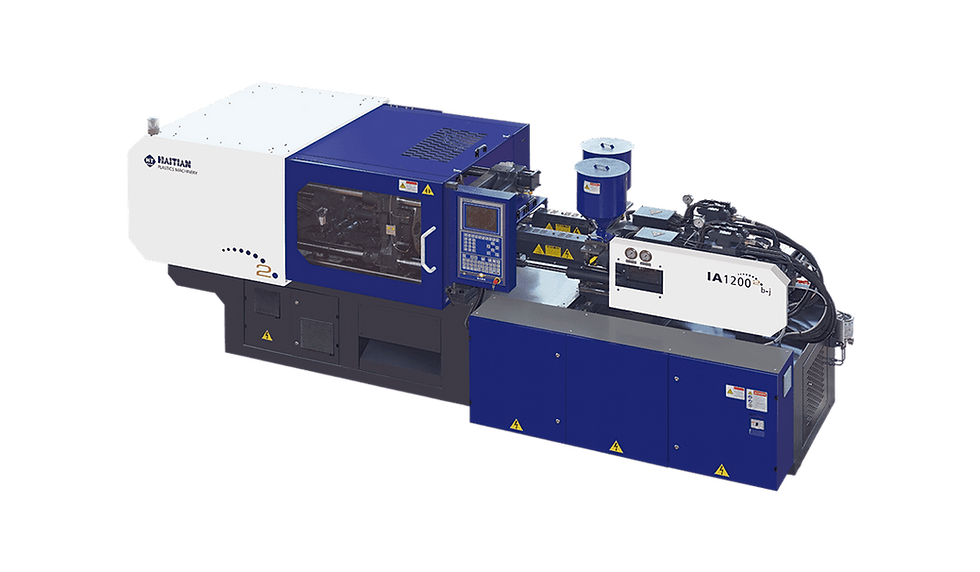
The following are the main categories of plastic molding machines:
Injection molding machines use high pressure to pump molten plastic into a mold cavity. The mold opens to release the completed object after the plastic has cooled and solidified. Injection molding is frequently used to create intricately designed containers and bottle caps, among other complex and accurate components.
Blow Molding Machines, In blow molding, a heated plastic parison, or hollow tube, is inflated inside a mold cavity until it takes on the shape of the mold. Hollow plastic items, such as bottles and containers, are frequently made using this technique.
Rotational molding machines, also referred to as rotomolding, use a heated mold that rotates along two perpendicular axes to hold powdered plastic. When the molten plastic cools, it forms a hollow product that covers the inside of the mold. Tanks, containers, and other large, hollow objects are best produced using rotational molding.
Thermoforming machines, To create the desired shape, a plastic sheet is heated until it becomes malleable and then stretched over a mold. The finished product is made by trimming the molded plastic once it has cooled. Disposable cups, trays, and packaging materials are frequently made using this technique.
The Manufacturing Process of Plastic Containers
The production of plastic containers involves several key steps, each tailored to the specific molding technique employed:
Material Selection and Preparation:
Depending on the desired qualities of the finished product, the process starts with the selection of suitable plastic resins, such as polyethylene terephthalate (PET), high-density polyethylene (HDPE), or polypropylene (PP). After that, the selected resin is prepared typically in pellet form and put into the molding machine.
Melting and Molding:
In injection molding, plastic pellets are heated to a molten state before being forced under intense pressure into a mold cavity. Blowing air into a parison that has been extruded and trapped in a mold allows it to take on the shape of the mold. In order to uniformly coat the inner surfaces, plastic powder is heated within a revolving mold during the rotational molding process.
Cooling and Ejection:
The plastic is chilled to solidify once it has taken on the shape of the mold. Depending on the molding process, different cooling techniques may be used, such as water or air cooling systems. The newly created plastic container is expelled from the mold when it has solidified.
Trimming and Finishing:
To improve the container's look and performance, post-molding procedures may involve cutting away extra material, applying labels, or applying surface treatments.
The Role of Plastic Molds in the Plastic Industry

Because they specify the final product's shape and characteristics, plastic molds are essential parts of the production process. Molds are carefully crafted and usually composed of sturdy materials like steel or aluminum to endure the high heat and pressures involved in molding operations. To guarantee constant quality and production efficiency, a mold's design must take into consideration elements like material flow, cooling rates, and ease of ejection.Technological developments in mold-making, such as computer-aided design (CAD) and computer-aided manufacturing (CAM), have improved the accuracy and intricacy of molds, enabling the production of sophisticated and personalized plastic goods.
Applications and Significance in the Plastic Industry
A wide variety of plastic items may now be produced thanks to the plastic industry's transformation brought about by the adaptability of plastic molding machines. The ability to mass-produce reliable and long-lasting plastic containers has simplified manufacturing procedures and decreased prices for anything from common household products to specialist industrial components.
Plastic containers, for example, are lightweight, strong, and reasonably priced options for storing and shipping items in the packaging industry. Because molding technologies are so versatile, producers may create containers with a wide range of sizes, forms, and features to meet the demands of the market.
Sustainability Considerations in Plastic Manufacturing
The plastics sector is putting more and more emphasis on sustainable methods as environmental concerns about plastic waste increase. Innovations like recycling programs, biodegradable plastics, and the creation of environmentally friendly materials are becoming more popular. For instance, businesses are investigating the use of recycled polymers in production procedures and creating goods that are more easily recyclable. Furthermore, improvements in molding technology are intended to lower material waste and energy usage, supporting more environmentally friendly production practices.
Conclusion
Using advanced plastic molding equipment and a variety of molding techniques, the production of plastic containers is a complicated but incredibly effective operation. High-quality plastic items that are essential to many industries are produced thanks to the incorporation of accurate plastic molds. Adopting sustainable practices and technical innovations will be essential to the plastics industry's continued evolution in order to satisfy consumer needs and solve environmental issues.
Comments