How Injection Molding Powers Industries: Automotive, Medical, Consumer, and More
- Haitian
- Apr 5
- 4 min read
Updated: Apr 9
Introduction
Injection molding has become the backbone of various industries, enabling the efficient production of high-quality plastic components. From automotive plastic components manufacturing to medical device injection molding, this process provides durability, cost-effectiveness, and precision. Whether it's electronics plastic parts production, logistics plastic solutions, or consumer goods plastic manufacturing, injection molding ensures mass production with consistency and minimal waste.
In this blog, we will explore how injection molding plays a critical role in industries like automotive, medical, packaging, electronics, logistics, consumer goods, and white goods plastic components manufacturing.
The Role of Injection Molding in Automotive Plastic Components Manufacturing
The automotive plastic components manufacturing sector relies heavily on injection molding to produce durable and lightweight parts. Automotive manufacturers use this technology to create:
Dashboard panels
Bumpers and grilles
Door handles and trims
Interior and exterior lighting enclosures
Engine components
Injection molding offers benefits like weight reduction, improved fuel efficiency, and enhanced design flexibility. The use of high-performance polymers ensures that automotive plastic components withstand heat, impact, and wear over time.
Packaging Industry Injection Molding
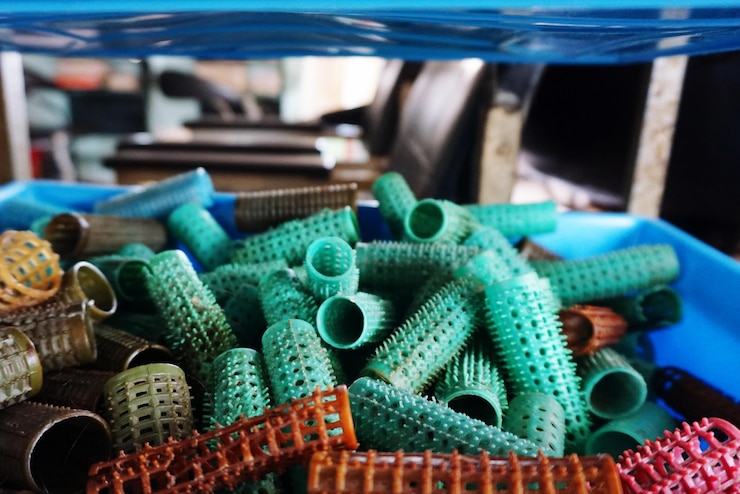
The packaging industry injection molding segment is another crucial application, offering efficient production for:
Plastic bottles and containers
Caps and closures
Food-grade packaging
Custom plastic packaging solutions
Injection molding in packaging helps manufacturers create lightweight, durable, and sustainable packaging options. Many businesses are now focusing on biodegradable and recycled plastics to reduce environmental impact while maintaining high-quality packaging standards.
Medical Device Injection Molding

The medical device injection molding industry demands precision and strict regulatory compliance. Medical manufacturers rely on this process to produce:
Syringes and IV components
Surgical instruments
Diagnostic test kits
Medical tubing and connectors
Implantable plastic devices
With advancements in medical-grade plastics, injection molding ensures biocompatibility, sterilization resistance, and accuracy in complex medical parts. Many facilities employ cleanroom injection molding to maintain hygiene and prevent contamination.
Electronics Plastic Parts Production
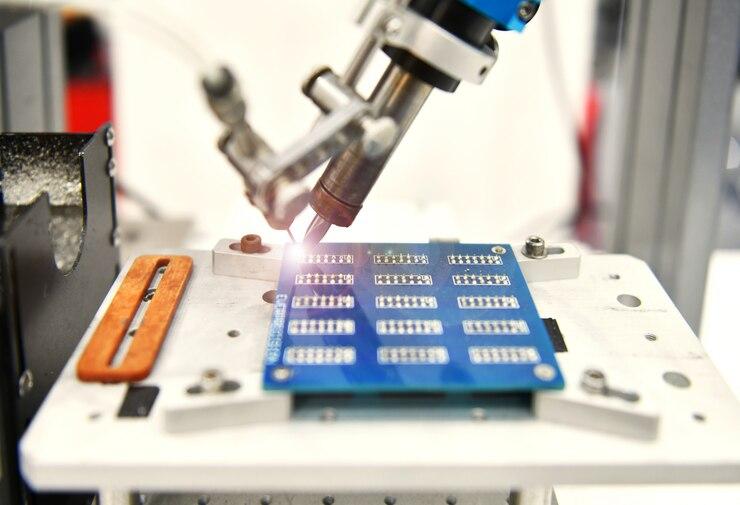
The electronics plastic parts production industry benefits from injection molding due to the need for precision and durability. Some of the commonly produced plastic parts include:
Smartphone and laptop casings
Electrical connectors
Circuit board housings
Remote control enclosures
Cable management components
Using advanced polymers such as ABS, polycarbonate, and flame-retardant plastics, manufacturers ensure that electronic components remain heat-resistant, lightweight, and impact-resistant.
Logistics Plastic Solutions

The logistics plastic solutions sector depends on injection molding for producing essential transportation and storage components, including:
Plastic pallets
Crates and bins
Storage containers
Protective packaging solutions
These plastic solutions help improve supply chain efficiency, durability, and cost-effectiveness. Injection-molded plastic logistics products are reusable, easy to clean, and lightweight, making them ideal for long-term transportation and storage needs.
Consumer Goods Plastic Manufacturing
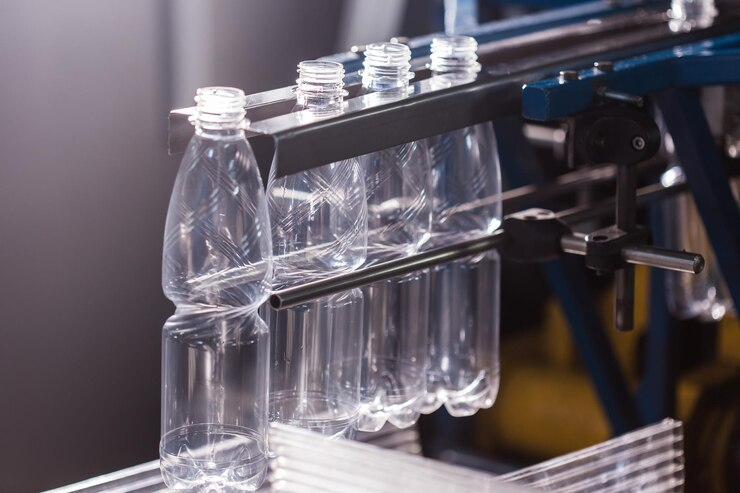
The consumer goods plastic manufacturing industry benefits significantly from injection molding due to its versatility in creating everyday products. This industry covers a broad range of items, such as:
Household plastic items
Toys and games
Kitchenware and utensils
Personal care product containers
Sporting goods
Injection molding allows manufacturers to produce high-quality plastic goods in bulk while maintaining design precision, durability, and affordability. As consumer demand shifts towards sustainable materials, many companies are incorporating recycled plastics into their manufacturing processes.
White Goods Plastic Components Manufacturing

The white goods plastic components sector focuses on household appliances and large domestic devices. Common applications include:
Washing machine drums and housings
Refrigerator door panels and shelves
Microwave oven casings
Vacuum cleaner components
Air conditioner parts
Plastic injection molding provides lightweight, durable, and heat-resistant components that enhance product longevity and energy efficiency.
Advantages of Injection Molding Across Industries
Regardless of the industry, injection molding offers numerous benefits:
High Efficiency & Speed – Once the mold is created, production cycles are fast, allowing for large-scale manufacturing.
Precision & Consistency – Injection molding ensures every part is identical, reducing defects and quality issues.
Cost-Effective for Mass Production – While initial tooling costs can be high, per-unit costs decrease significantly with larger production runs.
Material Versatility – From biodegradable plastics to high-performance polymers, injection molding accommodates various materials.
Reduced Waste & Sustainability – Many manufacturers now recycle excess plastic and use sustainable alternatives to reduce waste.
Automation Integration – Modern machines incorporate automation and robotic assistance for enhanced efficiency and reduced labor costs.
Future Trends in Injection Molding for Various Industries

As technology advances, several trends are shaping the future of injection molding across different industries:
Sustainable Manufacturing – The shift toward using biodegradable plastics and recycled materials continues to grow.
Smart Manufacturing – IoT-enabled machines provide real-time monitoring, predictive maintenance, and process optimization.
Lightweighting Innovations – The focus on reducing plastic component weight without sacrificing durability is gaining traction.
Advanced Materials – Development of high-performance and eco-friendly polymers for specialized applications is expanding.
Automation & AI Integration – AI-driven quality control and robotic handling are becoming standard features in modern injection molding facilities.
Injection molding plays a vital role in automotive plastic components manufacturing, packaging industry injection molding, medical device injection molding, electronics plastic parts production, logistics plastic solutions, consumer goods plastic manufacturing, and white goods plastic components. The ability to produce durable, cost-effective, and high-quality plastic components has made this process indispensable across industries.
As companies move toward sustainability, automation, and precision engineering, the future of injection molding continues to evolve. Businesses looking to invest in this technology should focus on innovation and efficiency to stay competitive in their respective markets.
Comments